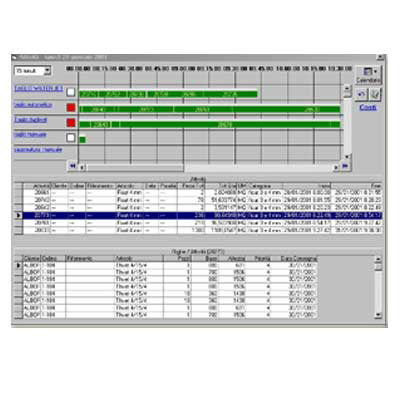
Perfect Gepro, in base ai dati degli ordini introdotti tramite Perfect Gea, ottimizza le sequenze di lavorazione dei vari centri (taglio, molatura, etc), tenendo conto della scadenza, dell’ingombro del materiale, degli straordinari richiesti e delle zone di consegna.
Viene proposto un piano di taglio comunque alterabile da parte dell’operatore. In base al piano definito, all’atto dell’immissione di un ordine, il sistema propone la data di scadenza nell’ipotesi che le attività relative all’ordine siano eseguite in coda a quelle già pianificate.
In collaborazione con Perfect Monit, modulo per il monitoraggio della produzione, rileva l’avanzamento delle commesse tramite terminali muniti di lettore di bar code posti nei centri di lavorazione. Il Monitoraggio così eseguito permette anche una stima corretta delle potenzialità di produzione di ciascuna risorsa, sia ad uso del modulo di programmazione della produzione, che nell’analisi dei costi.
Pianificazione della produzione
All’atto del caricamento di un ordine, il controllo automatico delle disponibilità di magazzino permette di segnalare automaticamente l’eventuale mancanza del materiale o l’impegno dello stesso già per commesse precedenti; viene indicata automaticamente dal sistema la possibile data di consegna, tenendo conto del piano di produzione a quel momento previsto e le priorità fino al momento definite.
Il controllo a video, possibile in ogni momento, dello stato di avanzamento della commessa, permette di rispondere immediatamente al cliente, senza bisogno di andare in produzione e sentire dai vari addetti a che punto è quella commessa. Il sistema fornisce, in tempo reale, la data di consegna prevista e, a livello più dettagliato, a che reparto è ferma ciascuna riga d’ordine.
Lo schedulatore della produzione crea il piano delle attività previste per ogni risorsa. Esso ottimizza il costo complessivo aziendale, tenendo conto di costi effettivi (straordinari, ingombri del materiale) e stimati (l’insoddisfazione del cliente quando la commessa viene consegnata oltre la scadenza prevista).
In particolare determina:
1. Un migliore sfruttamento dello spazio per certe aree critiche, minimizzando l’ingombro nelle aree di magazzino dei semilavorati.
2. Una migliore gestione delle spedizioni in aree meno servite, in quanto il piano di produzione tiene conto della zona di consegna e fa in modo che la spedizione di una commessa sia pronta ad essere eseguita quando c’è un camion che serve quella zona.
3. Una migliore integrazione con l’ottimizzazione del taglio. Mentre con un gestionale classico si possono inviare ordini completi all’ottimizzatore, tramite la scomposizione degli ordini in attività si considerano le singole righe per determinare un “progetto” di taglio: ad esempio se un ordine contiene pezzi che devono essere mandati alla tempera e altri no, è bene che i pezzi da inviare alla tempera siano tagliati molto prima degli altri, in modo che siano pronti per la spedizione più o meno allo stesso momento.
4. Una maggiore soddisfazione del cliente (risposta sempre pronta sui tempi di consegna previsti, sia all’atto dell’ordine che in ogni momento; migliore affidabilità delle previsioni fatte; tempestività nella eventuale segnalazione di ritardi; garanzia che nulla sia “dimenticato”).
5. Una migliore gestione dei turni e degli straordinari.
6. Complessivamente una riduzione dei costi aziendali e un aumento dell’efficienza.
Il piano generato identifica un certo numero di indici del buon andamento aziendale: il livello di utilizzo degli straordinari; il numero di ore libere per risorsa; il grado di saturazione delle risorse nel tempo; lo stesso grado di saturazione delle risorse tenendo conto delle sole attività già in ritardo. Gli ultimi due sono indici apparentemente simili ma in realtà opposti: il primo dovrebbe attestarsi al 100% su tutte le risorse (l’azienda deve produrre al massimo per sostenere i suoi costi fissi) mentre la seconda dovrebbe essere prossima allo zero (nessuna attività dovrebbe essere in ritardo rispetto alla data comunicata al cliente). I due grafici insieme riescono a dare un’idea abbastanza buona dell’andamento aziendale.
Verificando l’andamento aziendale si possono ipotizzare interventi correttivi: aumento (o riduzione) degli straordinari, i turni di produzione; acquisto (o rilascio) di nuove risorse in termini di addetti e macchine; aumento (o riduzione) dei prezzi, in particolare tenendo conto della criticità di specifiche risorse; decisioni nei riguardi della politica verso gli agenti; pianificazione di interventi di manutenzione preventiva.
Condividi l'articolo
Scegli su quale Social Network vuoi condividere